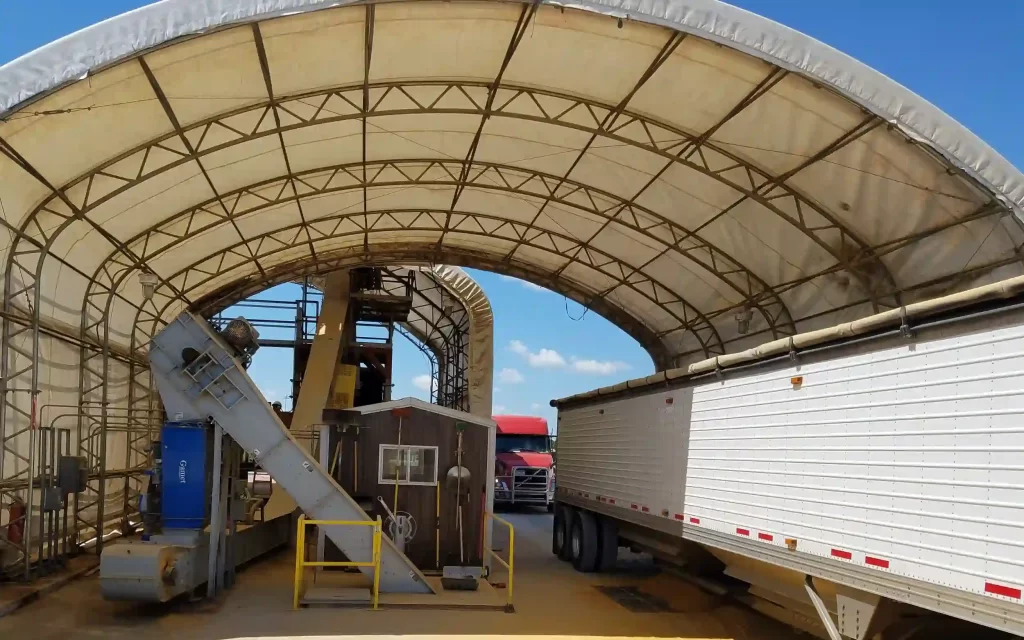
The Hidden Chaos of Bulk Transloading Yards
Bulk transloading is a high-stakes, high-volume operation where precision and efficiency make all the difference. Whether handling grain, fuel, chemicals, aggregates, or other bulk commodities, transload yards are critical transfer points in supply chains. One misstep—delayed railcar unloading, inefficient truck movement, or a lack of tracking—can create costly bottlenecks that ripple through an entire operation.
Yet, many bulk transloading yards still rely on manual tracking methods, spreadsheets, and outdated communication tools to manage workflows. While these approaches may have worked in the past, today’s fast-paced logistics environment demands real-time visibility, automation, and seamless coordination—which is where a Yard Management System (YMS) comes in.
In this guide, we’ll break down how YMS technology can transform bulk transloading operations, reduce costs, and optimize efficiency in ways that many in the industry have yet to fully embrace.
What is Bulk Transloading?
Bulk transloading is the process of moving bulk materials between different transportation modes, such as rail-to-truck, truck-to-rail, or ship-to-truck transfers. These yards serve as critical hubs where cargo is temporarily stored, processed, or transferred before reaching its final destination.
Common bulk transloading operations include:
🚛 Agricultural Commodities – Grain, fertilizer, and animal feed transferred between trucks and railcars.
⛽ Energy & Chemicals – Crude oil, refined fuels, liquid chemicals, and compressed gases.
🏗 Construction Materials – Sand, cement, aggregates, and asphalt.
🛢 Industrial Raw Materials – Plastics, metal ores, and recycled materials.
🛳 Maritime & Inland Ports – Bulk commodities transferred from barges or vessels to land-based transport.
These facilities often handle highly regulated and time-sensitive cargo, making precision and tracking essential for safety and compliance.

Challenges in Bulk Transloading Yard Operations
Without proper management, bulk transloading yards become chaotic, inefficient, and costly. Some of the biggest operational headaches include:
1. Slow Movement to Pits and Scales
- Moving bulk materials to and from pits and scales requires frequent manual communication
- Without a centralized system, transload yards struggle to maintain real-time inventory visibility.
2. Inefficient Railcar and Truck Coordination
- Many facilities rely on manual check-ins, leading to slow loading/unloading.
- Without optimized scheduling, trucks may arrive too early (causing congestion) or too late (leading to demurrage fees).
3. Excessive Dwell Time and Demurrage Costs
- Bulk railcars often sit idle too long due to miscommunication or lack of prioritization.
- Unnecessary delays rack up demurrage fees, significantly increasing operational costs.
4. Safety & Compliance Risks
- Hazardous materials require strict safety protocols—mismanagement can lead to fines, accidents, or even environmental disasters.
- Regulatory reporting and audits become difficult without accurate digital records.
5. Lack of Real-Time Visibility
- Yard supervisors often rely on walkie-talkies and whiteboards to direct workers.
- Without a single source of truth, miscommunications between dispatch, yard workers, and transportation providers cause costly mistakes.
In an era where supply chain disruptions are a daily reality, these inefficiencies can no longer be ignored. That’s where a Yard Management System changes the game.
How a YMS Optimizes Bulk Transloading Operations
A Yard Management System (YMS) solves these challenges by digitizing, automating, and optimizing yard processes. Here’s how:
1. Real-Time Inventory & Asset Tracking
✅ Tracks bulk material quantities, locations, and movement status within the yard.
✅ Provides live updates on which railcars, trucks, or storage tanks contain specific materials.
✅ Streamlines movements to pits and scales, providing users with a simple interface to accomplish their tasks.
2. Railcar & Truck Scheduling Optimization
✅ Automates appointment scheduling, reducing truck congestion and improving turnaround times.
✅ Syncs inbound rail schedules with truck pickups, ensuring cargo isn’t sitting idle.
✅ Reduces detention and demurrage fees by optimizing asset movement.
3. Faster Check-Ins and Gate Management
✅ Digitizes gate check-in processes, eliminating manual paperwork delays.
✅ Uses RFID, GPS, or mobile check-in apps to identify inbound/outbound trucks and railcars.
✅ Improves security by ensuring only authorized personnel and vehicles access the yard.
4. Compliance & Safety Management
✅ Automates hazmat tracking and regulatory reporting.
✅ Ensures adherence to environmental and safety regulations with built-in compliance checks.
✅ Reduces accidents by preventing unauthorized yard movements through geofencing and automated alerts.
5. Integration with Software (ERP, TMS) and Hardware (scales)
✅ Syncs with Enterprise Resource Planning (ERP) systems for accurate inventory and billing.
✅ Connects to Transportation Management Systems (TMS) to coordinate inbound/outbound shipments.
✅ Seamlessly ties in with scales for weighing loads, recording cargo weights automatically.
The Business Impact of YMS in Bulk Transloading Yards
Companies that implement a Yard Management System in bulk transloading yards report significant operational improvements:
📉 Up to 40% reduction in railcar and truck dwell times
📉 90% fewer detention and demurrage fees
📉 20% faster material transfer operations
📉 Improved safety compliance and reduced incident rates
📉 More accurate inventory control, reducing loss and waste
By eliminating manual inefficiencies, a YMS ensures that bulk cargo moves faster, safer, and at lower costs—giving transload facilities a major competitive advantage.
Choosing the Right YMS for a Bulk Transloading Yard
Not all Yard Management Systems are designed for bulk transloading. Here’s what to look for:
🔹 Bulk Inventory Management Capabilities – Can it track granular cargo (e.g., volume or weight instead of item counts)?
🔹 Pit and Scale Features – Does it have specific pit and scale features to streamline movements and divvy out tasks?
🔹 Rail & Truck Integration – Can it sync with rail and trucking schedules to optimize inbound/outbound movements?
🔹 Automated Gate Check-Ins – Does it offer check-in via kiosk or QR code scanning capabilities to streamline the gate in process?
🔹 Compliance Features – Does it provide regulatory reporting and hazardous material tracking?
🔹 Scalability – Can it handle large-scale bulk transfers across multiple facilities?
Conclusion: The Time to Modernize is Now
Bulk transloading operations are too critical—and too costly—to rely on outdated yard management methods. Whether handling agriculture, energy, construction, or industrial materials, implementing a Yard Management System can:
✅ Reduce dwell times and eliminate costly delays
✅ Improve inventory accuracy and prevent lost cargo
✅ Enhance safety and regulatory compliance
✅ Optimize truck and rail scheduling for peak efficiency
As the industry moves toward digitization and automation, investing in a YMS is no longer optional – it’s a competitive necessity.