NEWS PROVIDED BY
Jason Colasante, LinkedIn
Feb 18, 2025
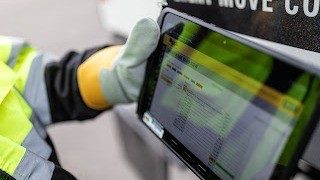
Grocery retailers face several key challenges in their distribution center (DC) operations, especially when it comes to optimizing efficiency and managing costs. Let’s break these challenges down and explore how a Yard Management System (YMS) can help address each one:
1. Trailer Dwell Time
Challenge:
- Trailer dwell time refers to how long a trailer stays in the yard before being loaded, unloaded, or moved. Excessive dwell time can cause bottlenecks, delaying the overall distribution process and reducing the throughput of goods.
- For grocery retailers, this is a significant issue, as delays in the yard often translate to delays in getting perishable goods to stores, leading to potential spoilage.
How YMS Can Address This:
- A Yard Management System (YMS) can help reduce trailer dwell time by offering real-time tracking of trailers and optimized scheduling for both incoming and outgoing deliveries.
- YMS can use data-driven algorithms to match trailers with appropriate docks at the right time, ensuring trailers are unloaded and loaded quickly.
- It can also allow the retailer to prioritize time-sensitive shipments, especially for perishable goods, reducing the risk of delays.
- By providing visibility into yard operations, the system can help manage trailer flow, reducing unnecessary congestion and bottlenecks.
2. Loss of Perishable Goods
Challenge:
- Perishable goods like fruits, vegetables, dairy, and meat have a limited shelf life, and any delays in transportation or warehouse operations can lead to spoilage and financial loss.
- The risk of temperature fluctuations or improper handling during the transfer from trailer to distribution center (DC) is also a significant concern.
How YMS Can Address This:
- A YMS can integrate with temperature-monitoring systems in real-time, ensuring that trailers and goods are maintained at the correct temperatures throughout the yard.
- YMS can also provide alerts when perishable goods are at risk of spoiling, ensuring that action is taken to prioritize those shipments and move them through the yard faster.
- By streamlining the flow of goods and improving coordination between yard operations and the warehouse, the system reduces the likelihood of delays that can lead to spoilage.
3. Overspending on Transportation
Challenge:
- Grocery retailers often face high transportation costs due to inefficiencies in fleet management, long routes, poorly planned delivery schedules, or underutilized trailers.
- Overspending can also result from the failure to optimize the use of the existing fleet, leading to unnecessary costs for carriers and the business.
How YMS Can Address This:
- A YMS can optimize transportation routes by integrating with route-planning tools that analyze traffic, weather, and demand, leading to more efficient transportation.
- It can help retailers ensure full utilization of trailers, reducing the need for extra shipments and minimizing wasted space.
- By providing better visibility of trailer and load availability, the YMS can help coordinate shipments, reducing the need for last-minute emergency transport that often carries a higher cost.
- Integration with Transportation Management Systems (TMS) can provide end-to-end optimization, improving transportation planning, reducing costs, and increasing the efficiency of deliveries.
Additional Ways YMS Can Improve Distribution Center Operations:
- Resource Optimization: YMS can help optimize yard workers and equipment by providing insights into where resources are most needed, reducing idle time and increasing throughput.
- Real-Time Visibility: A comprehensive YMS provides real-time updates on trailer status, locations, and task assignments, allowing the retailer to make informed decisions and adapt quickly to any operational changes.
- Automation: YMS can integrate with automated systems (e.g., Automated Guided Vehicles, RFID) to streamline operations and reduce manual effort.
By leveraging these YMS capabilities, grocery retailers can significantly improve operational efficiency, reduce waste, and minimize costs, addressing key challenges in distribution center operations.